Hybrid ceramic bearings represent a significant advancement in bearing technology, offering superior performance compared to traditional steel bearings. In this comprehensive guide, we will delve into the world of hybrid ceramic bearings, exploring their construction, benefits, applications, and how they can revolutionize various industries. Whether you are an engineer, a machinery enthusiast, or just curious about this cutting-edge technology, read on to discover the exciting world of hybrid ceramic bearings.
The key components of hybrid ceramic bearings are:
(1) Ceramic Balls
The rolling elements in these bearings are made from high-quality ceramic materials such as silicon nitride (Si3N4) or zirconia (ZrO2). These materials offer exceptional hardness, corrosion resistance, and low friction properties.
(2) Steel
The outer and inner raceways, or rings, are typically made from steel. These rings provide durability and strength to the bearing structure.
2. What Are Hybrid Ceramic Bearings?
Hybrid ceramic bearings are a type of rolling-element bearing that combines elements of both traditional steel ball bearings and ceramic materials. In a typical bearing, the rolling elements, such as balls or rollers, are made of steel. However, in hybrid ceramic bearings, the rolling elements are typically made of ceramic materials, while the inner and outer races (the parts that enclose the rolling elements) are still made of steel.
These materials offer several advantages over traditional steel bearings:
- High Hardness: Ceramic materials are harder than steel, which can result in increased durability and resistance to wear.
- Low Friction: Ceramic bearings can exhibit lower friction coefficients compared to steel bearings, potentially leading to reduced energy consumption and improved efficiency.
- Lightweight: Ceramic materials are generally lighter than steel, which can contribute to lower rotational mass and reduced centrifugal forces, particularly in high-speed applications.
- Corrosion Resistance: Ceramics are less susceptible to corrosion than steel, making hybrid ceramic bearings suitable for applications where exposure to harsh environments or corrosive substances is a concern.
- High Temperature Resistance: Ceramic materials can withstand higher temperatures than steel, making hybrid bearings suitable for applications involving elevated temperatures.
hybrid ceramic bearings
3. What is the Difference Between Ceramic and Hybrid Ceramic Bearings?
The main difference between ceramic bearings and hybrid ceramic bearings lies in the materials used for the rolling elements (such as balls) and, to some extent, the type of bearing races.
Here's a breakdown of each:
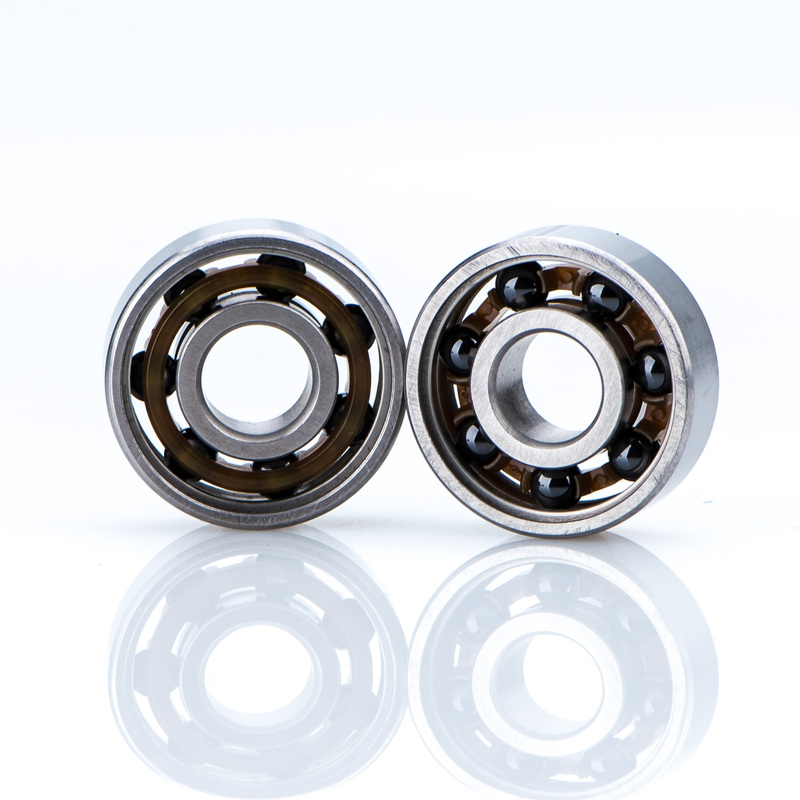
(1) Hybrid Ceramic Bearings
In hybrid ceramic bearings, only the rolling elements are made of ceramic material, while the inner and outer races are typically constructed from steel.
Common ceramic materials used for the rolling elements include silicon nitride (Si3N4) or zirconia (ZrO2).
Hybrid ceramic bearings aim to combine the advantages of ceramic rolling elements with the more traditional steel races, offering improved performance, reduced friction, and increased durability.
Hybrid ceramic bearings are often chosen for applications where the benefits of ceramic materials are desired, but a more cost-effective solution than full ceramic bearings is preferred.
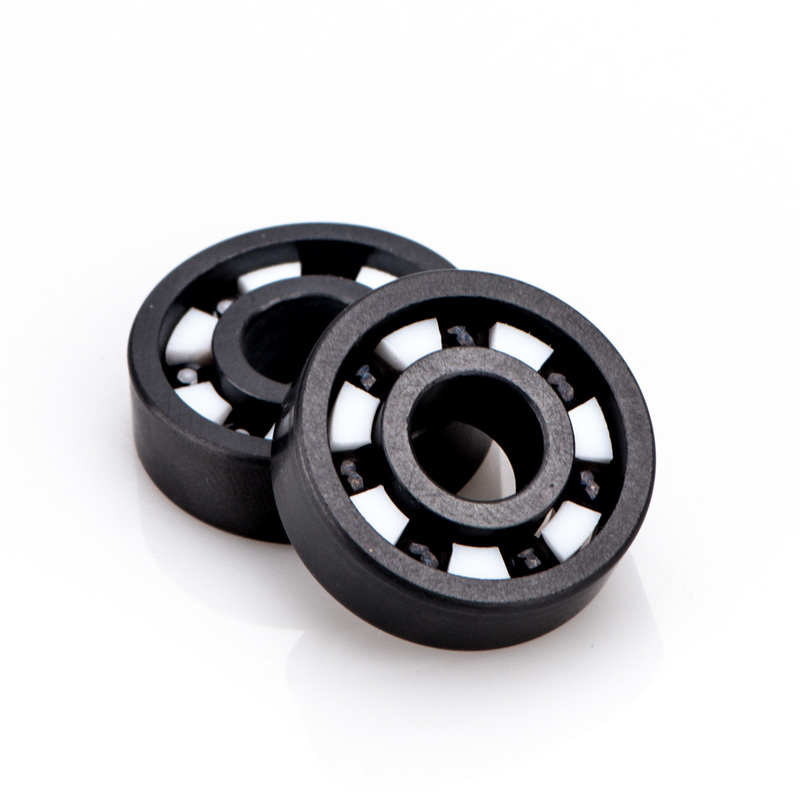
(2) Ceramic Bearings
In ceramic bearings, both the rolling elements (balls or rollers) and the bearing races (inner and outer) are made entirely of ceramic material, typically silicon nitride (Si3N4) or zirconia (ZrO2).
Ceramic bearings offer benefits such as high hardness, low friction, resistance to corrosion, and high-temperature tolerance.
They are often used in applications where these properties are critical, such as in high-performance and specialty industries, including aerospace and certain industrial machinery.
In summary, the primary distinction is that ceramic bearings are entirely made of ceramic material, both for the rolling elements and the races, while hybrid ceramic bearings incorporate ceramic rolling elements with steel races. The choice between the two depends on the specific requirements of the application, considering factors such as cost, performance, and environmental conditions.
Extended reading: Ceramic Bearings : Advantages and Applications in Precision Engineering
4. Do Hybrid Ceramic Bearings Need to Use Lubricating Oil?
Yes, hybrid ceramic bearings, like other types of bearings, generally require lubrication to operate efficiently and reduce friction. Lubrication helps to minimize wear, dissipate heat, and prevent corrosion in the bearing components. While ceramics themselves can have lower friction coefficients compared to steel, proper lubrication is still crucial for optimal performance and longevity of the bearing.
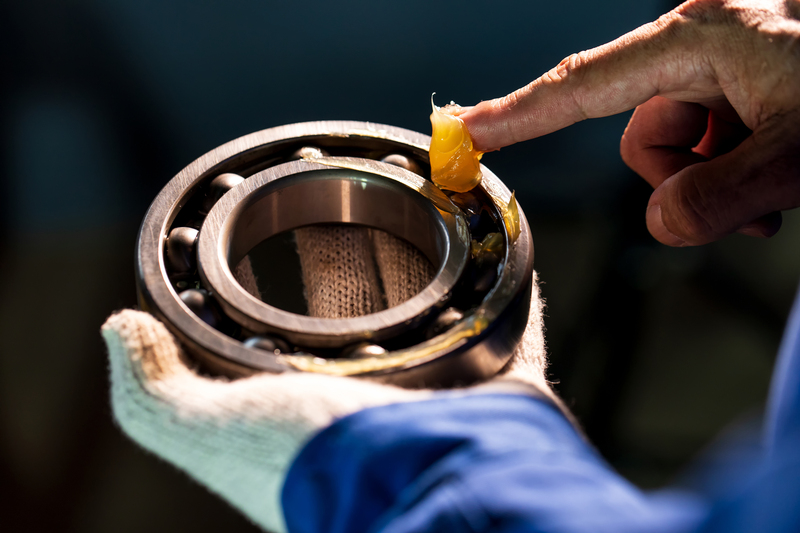
The choice of lubricant can vary depending on the specific application and operating conditions. Common lubricants for hybrid ceramic bearings include oils and greases. The selection of lubricant is influenced by factors such as the bearing speed, load, temperature, and environmental conditions.
Some advantages of using lubricating oil in hybrid ceramic bearings include:
-
Reduced Friction: Proper lubrication helps to reduce friction between the rolling elements (ceramic balls) and the raceways, contributing to improved efficiency.
-
Wear Protection: Lubricants form a protective film that helps prevent direct contact between the rolling elements and the races, reducing wear on the bearing surfaces.
-
Heat Dissipation: Lubricants aid in dissipating heat generated during operation, preventing overheating and potential damage to the bearing.
-
Corrosion Prevention: Lubricants can provide a protective barrier against corrosion, especially in applications where exposure to moisture or corrosive environments is a concern.
It's essential to follow the manufacturer's recommendations regarding lubrication type and interval for a specific hybrid ceramic bearing to ensure optimal performance and longevity. Regular maintenance, including lubricant inspection and replacement, is crucial for the continued smooth operation of the bearing.
5. Advantages of Hybrid Ceramic Bearings
(1) Reduced Friction
One of the most notable advantages of hybrid ceramic bearings is their ability to reduce friction significantly. The smooth surface of ceramic balls and their high hardness ensures minimal contact with the steel raceways. As a result, friction is reduced, leading to less heat generation and increased efficiency.
(2) Enhanced Durability
Ceramic materials are exceptionally hard and resistant to wear. This hardness helps hybrid ceramic bearings withstand heavy loads, shock loads, and abrasive environments better than traditional steel bearings. This translates into extended bearing life and reduced maintenance requirements.
(3) Corrosion Resistance
Hybrid ceramic bearings are highly resistant to corrosion, making them ideal for applications where exposure to harsh chemicals or moisture is a concern. They maintain their performance even in challenging environments.
(4) High-Speed Capability
Due to their reduced friction and lower heat generation, hybrid ceramic bearings are capable of operating at higher speeds than steel bearings. This feature makes them invaluable in applications requiring precision and high rotational speeds.
(5) Lower Operating Temperatures
Less friction means less heat generation during operation. Hybrid ceramic bearings run cooler, reducing the risk of overheating and improving the overall efficiency of machinery.
Hybrid ceramic bearings have revolutionized the world of bearings by combining the best attributes of ceramic and steel materials. Their reduced friction, enhanced durability, corrosion resistance, high-speed capability, and lower operating temperatures make them a superior choice for various applications across industries.
Investing in hybrid ceramic bearings can lead to improved machinery performance, reduced maintenance costs, and increased overall efficiency. As technology continues to advance, hybrid ceramic bearings are expected to play a pivotal role in shaping the future of many industries. If you're seeking to elevate your machinery's performance, it may be time to consider the remarkable benefits of hybrid ceramic bearings.
Further Reading:
Ceramic Bearings for Bicycles: The Choice for Enhanced Performance?
Is it really worth replacing with ceramic bearings?
Ceramic Bearings vs Steel Bearings: Performance and Differences
About ISK BEARINGS
Why is ISK BEARINGS frequently chosen as the specified bearing brand by major international companies?
This is just the tip of the iceberg!
Discover more about the features and applications of various bearings.
Click here to explore more articles and find the perfect bearing for your project.
The Comprehensive Guide to Needle Roller Bearings
Needle Bearings (Roller Bearings) are a type of bearing that performs exceptionally well at high speeds. Their rollers are precisely guided by specially shaped, high-rigidity cages with minimal dimensional error. Despite their small cross-section, needle bearings...
How Ball Bearing Works?
How Do Ball Bearings Work? Bearings are often small and unassuming components in a product, yet they are crucial for its proper functioning. Without bearings, many products would fail to operate effectively. But do you know how ball bearings...